Make the Difference?

Precision-Engineered Shapes

Customized Glass Composition

Uniform Quality and Consistency
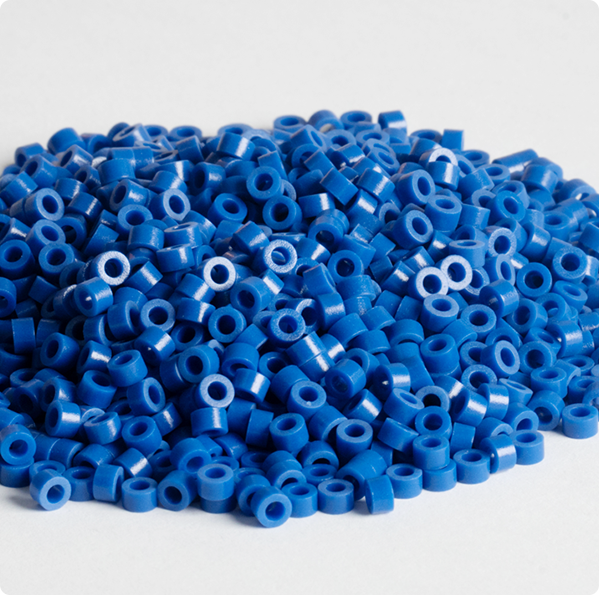
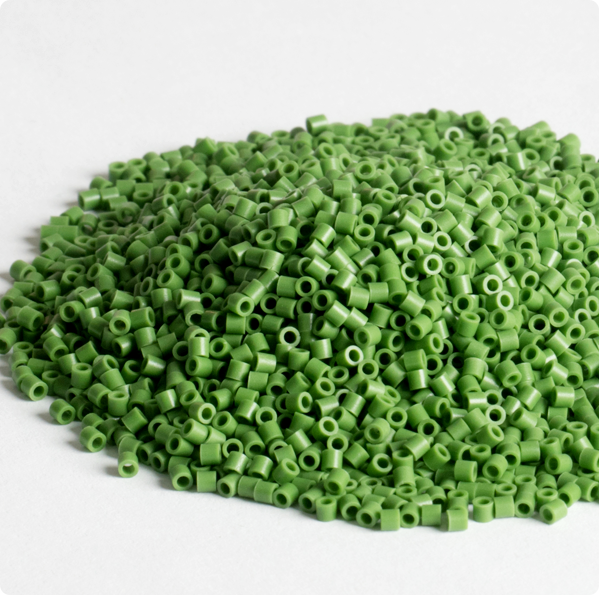
Your choice between granulated powder and glass preforms depends on your specific needs,
the capabilities of your manufacturing process, cost considerations, and convenience.
-
Glass Preforms
If you prefer convenience and simplicity, choosing glass preforms can streamline your manufacturing process. Ideal for when you don't have pressing capabilities in-house or when you want to bypass the complexities of pressing, preforms provide a ready-to-use solution that can significantly enhance efficiency and consistency.
-
Sealing Glass Powder
If you have your own pressing process and are looking for maximum control or aiming to reduce costs, granulated powder might be the right choice for you. This allows you to utilize your existing capabilities to create preforms exactly as you need them, offering unparalleled flexibility in design and production.
Process and Key Considerations
- Raw Material Selection
- Batch Preparation
- Forming the Preforms
- Precision Shaping
- Quality Control
- Packaging and Shipping
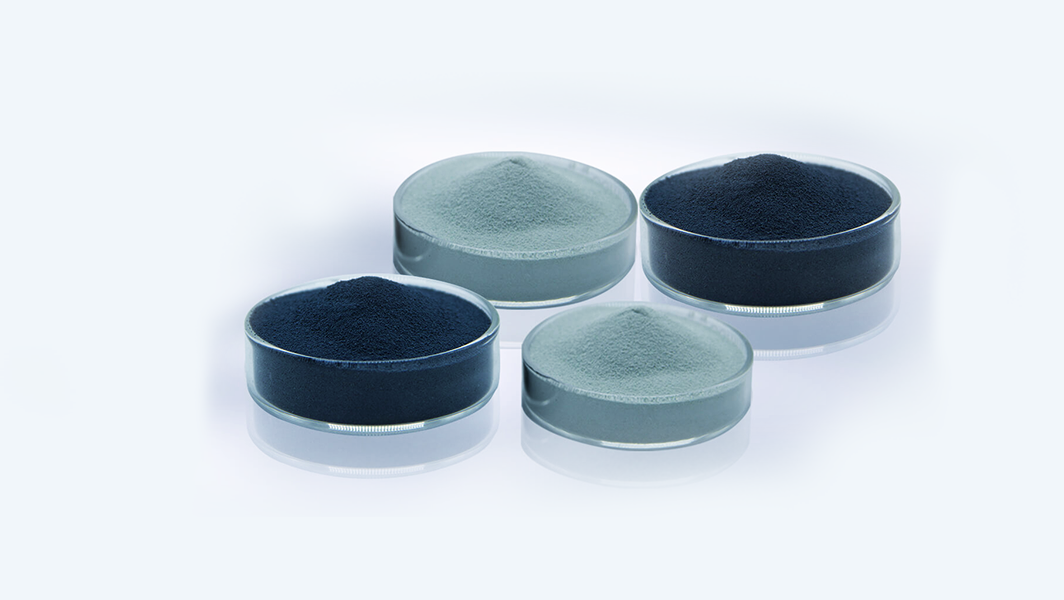
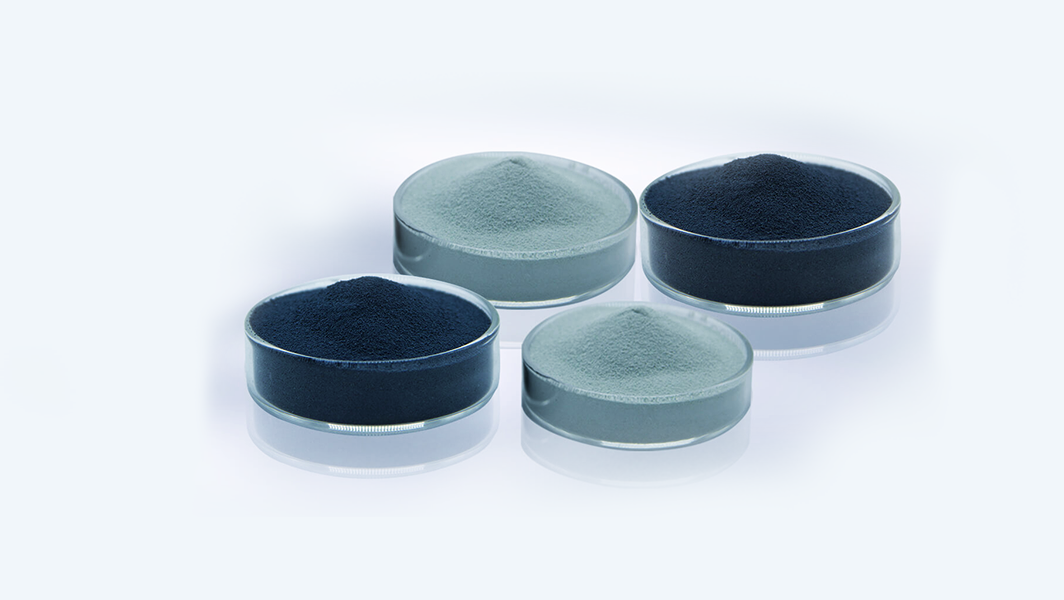
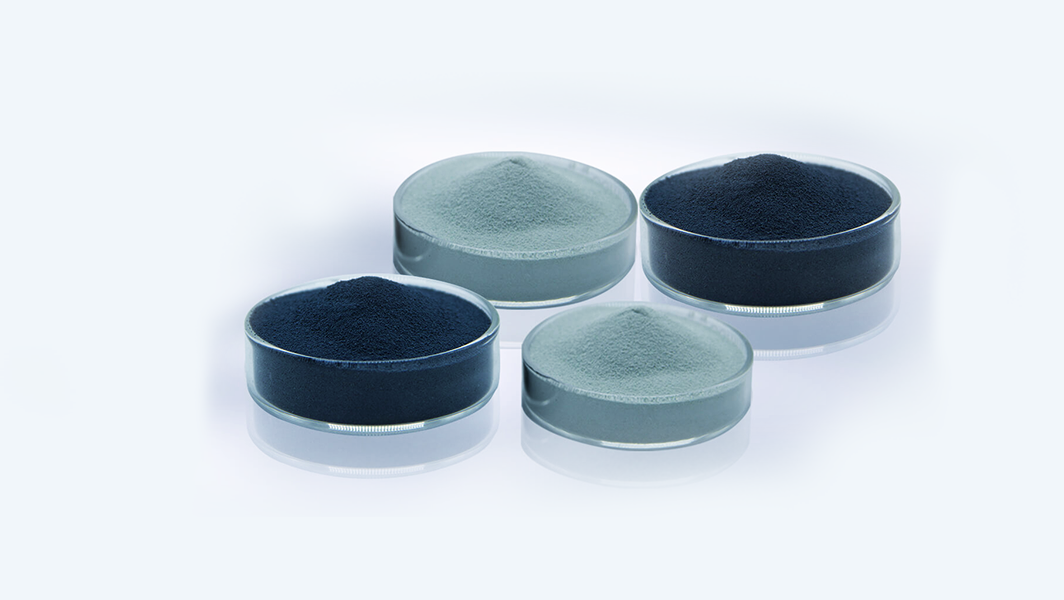
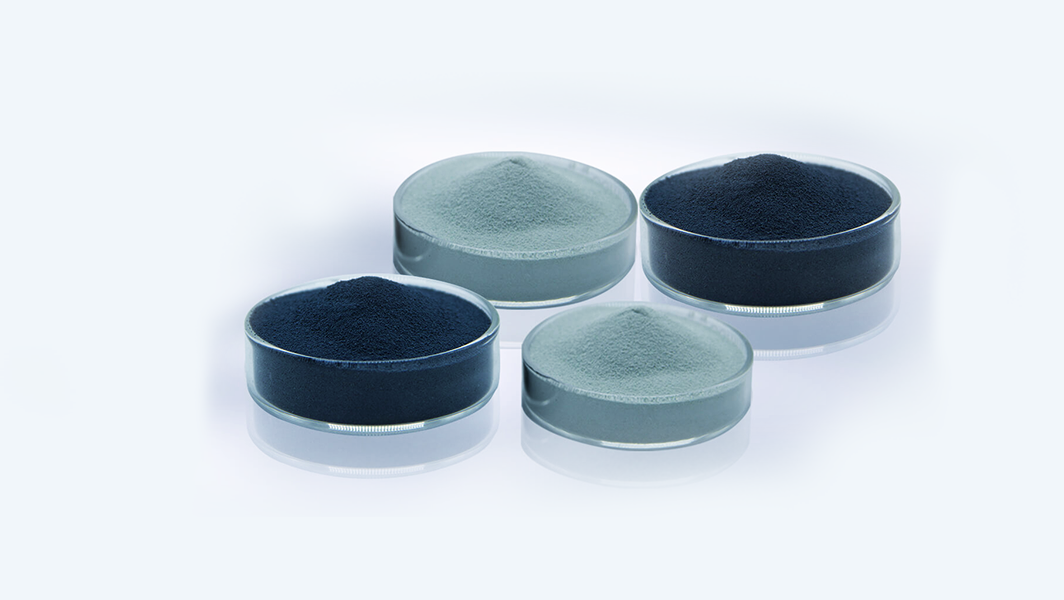
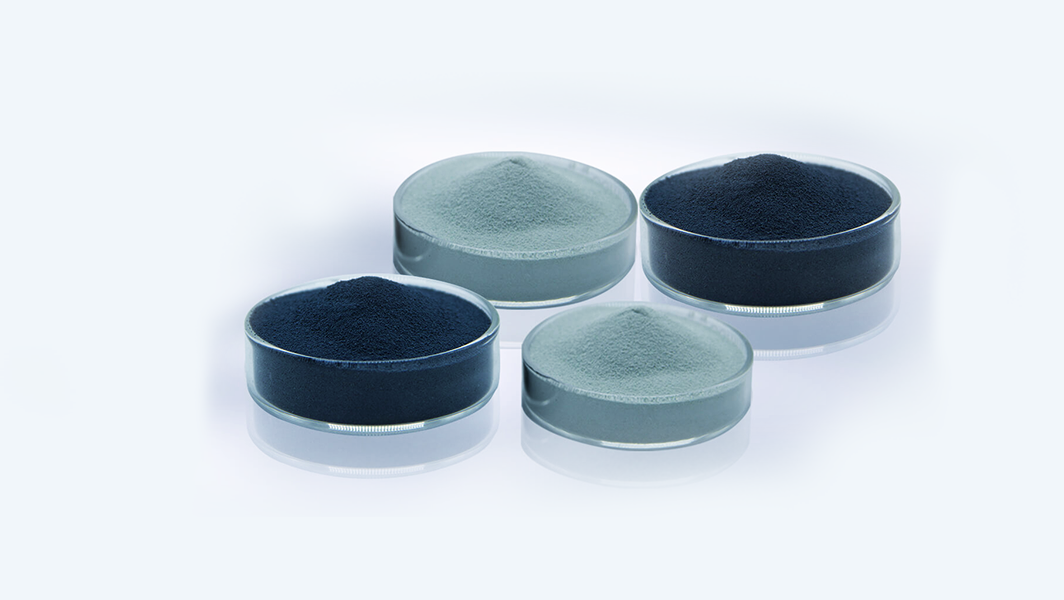
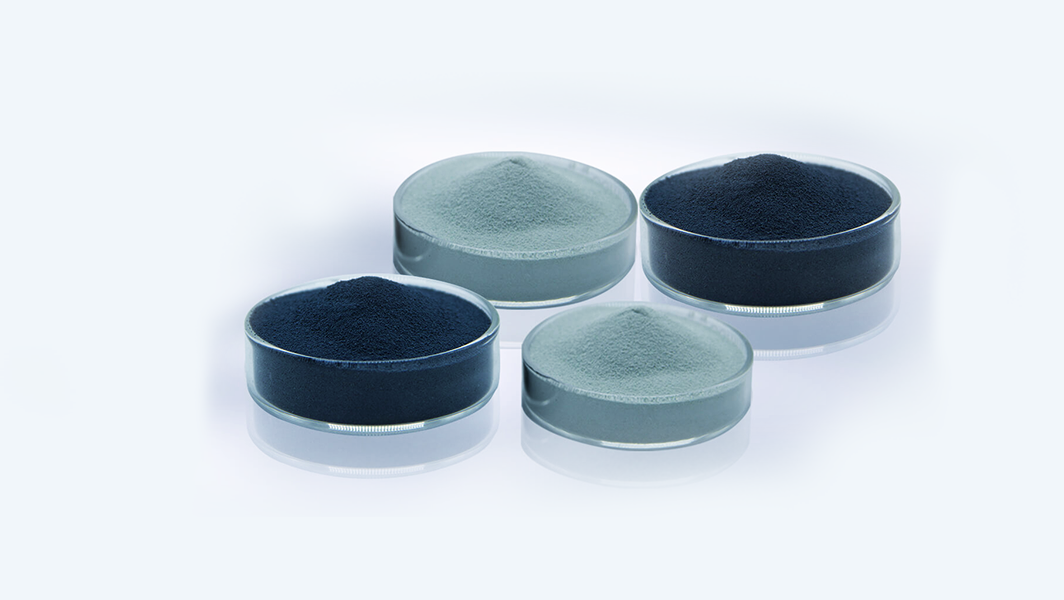
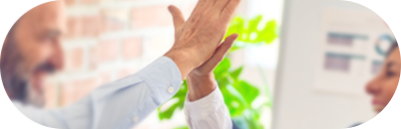
Product
